Welding Procedure Qualification for the fabrication of Pressure Equipment and Filter Internals in material grade Titanium Grade II & V according to ASME IX, ISO 15614-5 and client specifications.
All test results are accepted.
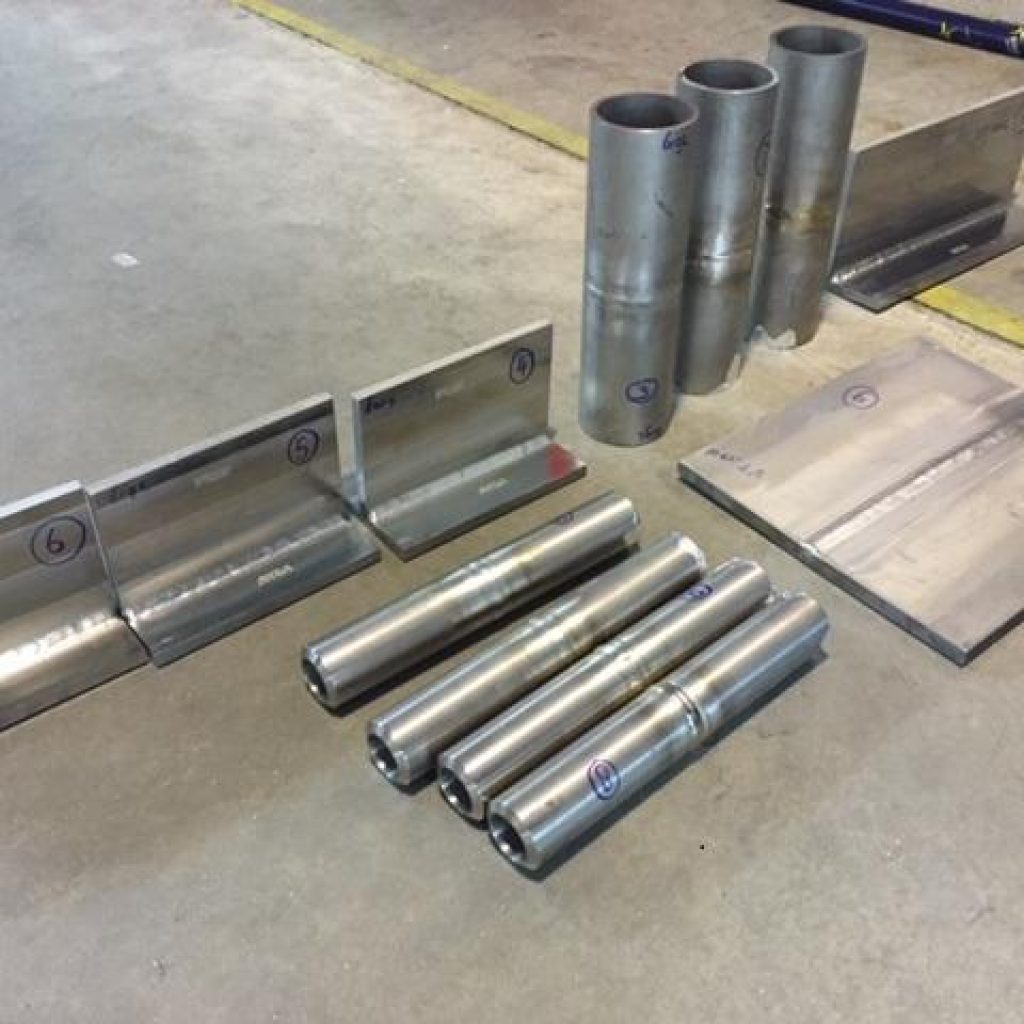
Despite the current corona virus, OMT is still going strong. Just like all other companies, we are facing a lot of uncertainties. We have taken the necessary measures to continue our business as safe as possible and we remain positive here at OMT.
Below picture shows a hydro static test in progress performed a few days ago. Two adsorber vessels (twins) designed and fabricated by OMT. Design code ASME VIII div 1 with code stamp and severe cyclic service design case. MOC for these vessels is carbon steel.
Again a project well done, finished in time with a happy customer as a result. Goods ready for painting.
You can reach us by phone and/or e-mail and we will keep on partnering with you.
To all: take good care of yourself and your loved ones.
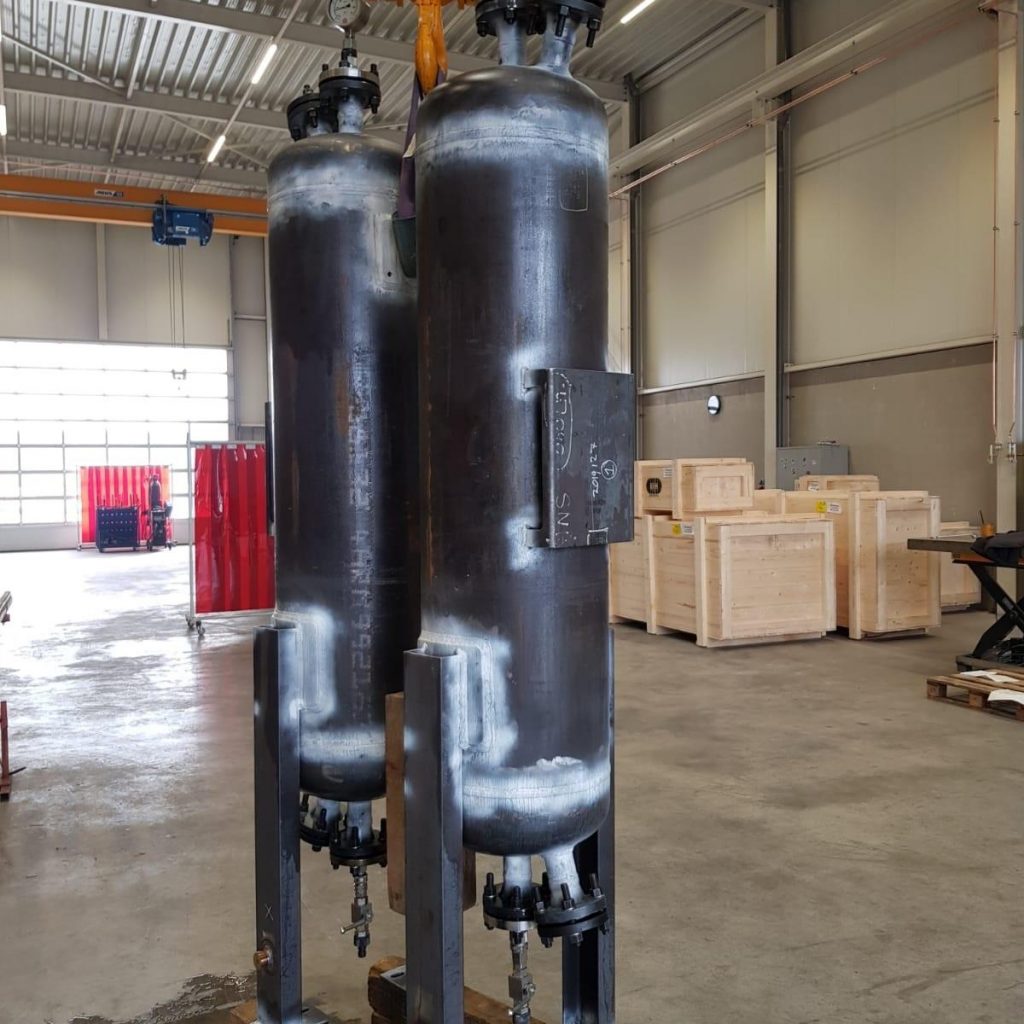
Ommeren Metaaltechniek has started with manufacturing a seperator vessel. The seperator vessel including internals will be used to seperate gasflows.
The design of the vessel will be according the ASME VIII div 1 and will also comply to the European PED 2014/68/EC guidelines for pressure vessels.
The complete vessel is manufactured out of stainless steel 304
In the video below you can see a part of the welding process on the seperator vessel
Ommeren Metaaltechniek has Cold Arc welding equipment available since February 2020.
This welding process is more efficient than other GMAW methods when the metal is thinner than 10 mm. The welding equipment detects a short circuit that sends a signal that causes the filler material to retract, cooling the seal time before each drop is placed. This leaves a smooth weld which is stronger than that of a hotter weld.
Recently we finished another great project, in which we fabricated several separator internals for a large refinery.
Several inlet devices, vertical vane packs for liquid/gas separation and some inlet sparger systems were fabricated by OMT.
Material of construction stainless steel, grade 316L, sour service application.
Engineering, manufacturing and welding professionals, partnering with you.
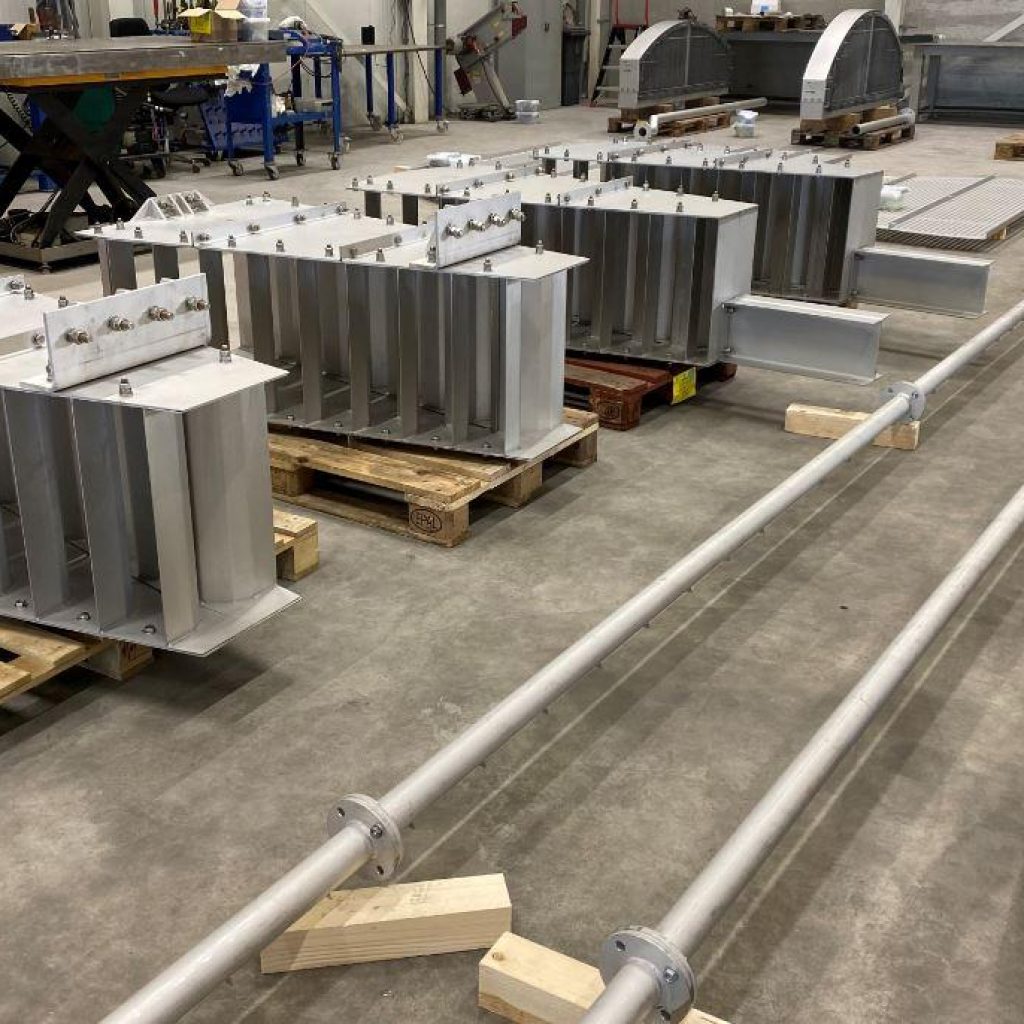
Final inspection of these pre-fabricated pressure parts with acceptance as result.
Stainless steel parts according to ASME VIII div 1 with part stamp and National Board registration will be used as Inlet Sections for Vent Silencers.
Engineering, manufacturing and welding by OMT.
Another well performed project by OMT with a happy customer as result, we don’t do it for less.
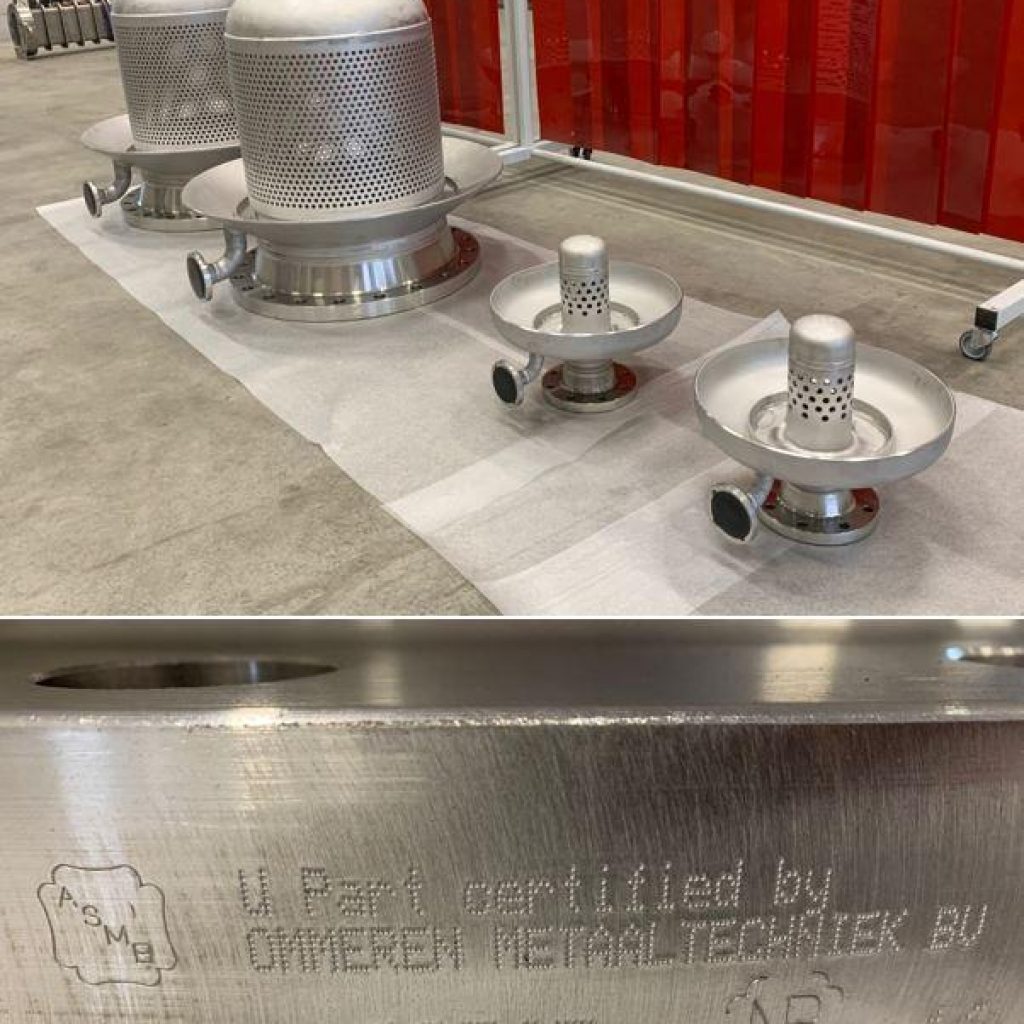
Just before the holidays, we completed another project and this bundle is now ready for packing and final shipment. OMT performed engineering, manufacturing, welding, testing and certification of this Hot Water / Waste Gas Heat Exchanger.
Design Code ASME VIII div 1, Code Stamped and client specifications. MOC Grade SS321.
Engineering, manufacturing and welding professionals, partnering with you.
Also in the need of process equipment? Contact our sales department.
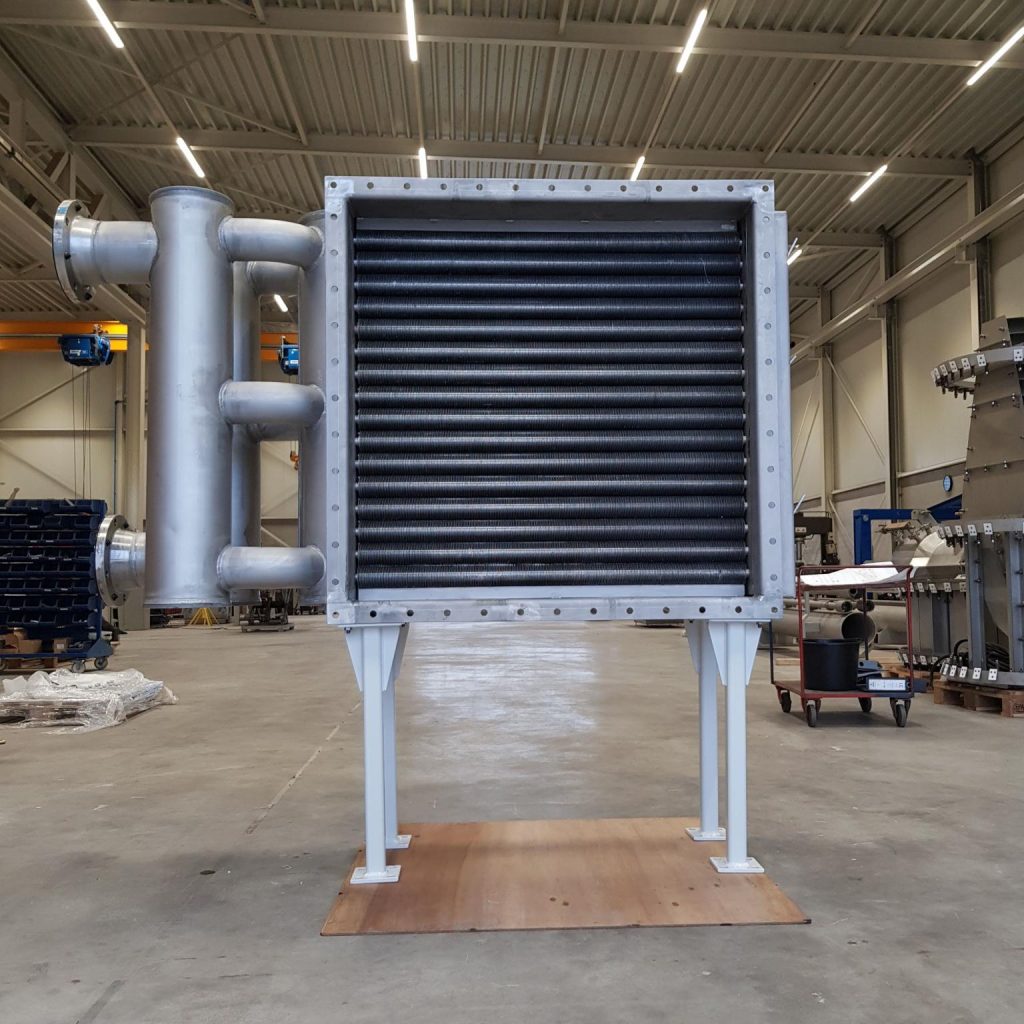
After various locations in the Ede region in the late 1990s and finally settling in 2007 at the Lorentzstraat in Ede, OMT expands its production facilities in 2019 with 1600 m2 of production area and 40 tons of crane capacity. As a result, OMT now has more than 3000 m2 at its current location.
Besides the focus on certification for the international supply of welded technical solutions, OMT has also expanded its engineering capacity.
In this way, OMT anticipates on the developments within the equipment construction, whereby OMT positions itself as a chain partner. Of course, we also anticipate on the ambitions of our current partners and this expansion has a positive impact on our product portfolio.
OMT realizes with its team of specialists a variety of projects in equipment construction for different markets, in which the welded technical solutions are central. In addition, OMT focuses on the automated welding of structures and assembled parts.
In close cooperation with our client and partner Cor Filtration, we completed a high profile project which consists of an Offshore Water Filtration Skid (Seawater Coarse Filtration Package) for the Cassia Compression Project in Trinidad Tobago. The filter package (6x6x4 mtr, 45 tons), is designed to filter incoming seawater for further use by other process equipment on the platform.
The offshore skid frame, pressure vessels, filter internals and connecting piping & manifolds are all designed and fabricated in house by OMT in accordance with many/intensive client specifications.
The filtration vessels are Amiad make, type Omega 54K and fully designed according to ASME VIII Div. 1 and delivered with ‘U’ certification. MOC for the vessels is super duplex (grades S32750/S32760) with extensive additional testing’s. Manifolds and piping designed and fabricated according to ASME B31.3, MOC also super duplex.